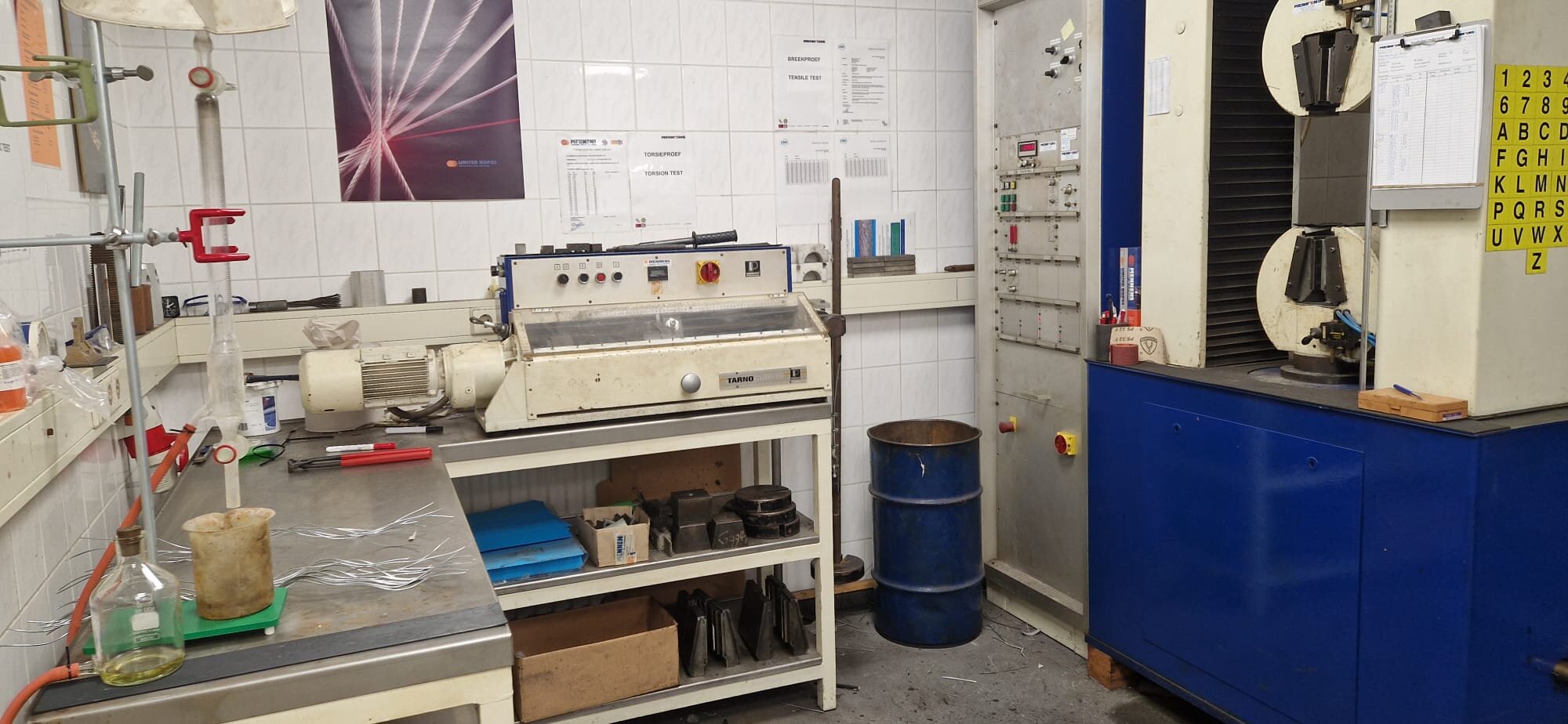
In many projects, steel cables must demonstrably comply with applicable standards. And insurers, inspection authorities, and other 'notified bodies' require that the cables be tested in advance. Do you want to know whether your steel cables meet the desired quality requirements? We are happy to assist you with, among other things, tensile tests, pre-stretching, magnetic rope testing and laboratory tests. Ruud Haag, Project Engineer, is happy to tell you more about the latter.
In our laboratory in Dongen, we test your cables before you put them into use. Usually, we test new cables, but we also test rejected cables. Then we check the expected remaining life to determine how much longer they could have lasted. Then our customers know where they stand in the future. From now on, the cables may be able to remain mounted in the system for longer, resulting in savings. This does not mean that you should automatically assume that your new cables will last longer. They must be inspected every year!
In the majority of cases, we carry out three tests in the lab: the wire drawing test (not to be confused with a tensile test of the entire steel cable), the torsion test and the zinc test. We conduct additional research on used steel cables. There's more about that later in this blog.
Wire by wire
We do not perform the three tests on the entire cable. We take off a piece of about fifty centimetres. We take this part completely apart: we untie each strand and all the individual strands again. We test the piece of steel cable wire by wire.
1. The wire drawing test
We start with the wire drawing test. We do this on a kind of mini-pull bench. We clamp the wire between the two ends of the tensile tester. They are then moved apart with a force of up to 100 kN (about 10,000 kg). If the thread breaks, the machine will stop automatically. We can perfectly measure how much pulling force is needed before the individual wire breaks. In this way, we test the tensile strength of the entire steel cable. And we check whether it meets the minimum breaking load.
2. The Torsion Test
The next test that the material undergoes is the torsion test. Also known as the twist test. We use this to test the stiffness and toughness of the material. And we immediately see the state of the zinc layer's adhesion. In case of poor adhesion, cracks appear in the material. In the torsion test, one side of the wire is held while the other side is rotated around its axis. Does it break with less than three turns? Then the material is brittle: old and worn.
3. The zinc test
Finally, each type of wire undergoes the zinc test. Is there still enough zinc on the steel to prevent it from rusting? To do this, we place a piece of wire in a column of hydrochloric acid. The hydrochloric acid bites into the zinc on the cable. This creates hydrogen which naturally rises to the top of the column. We close the top so that the hydrogen remains at the top and the remaining hydrochloric acid is pushed down. All the zinc has dissolved when you can no longer see gas bubbles forming. On the scale on the column, we can easily read how much hydrogen is in it. We use this to calculate how much zinc there was on the cable. This is also known as the zinc weight.
Additional research
As mentioned, we only perform the above tests on new cables. But we do additional research on used cables. We do this to determine the remaining life of the cable. And to find out the cause of the possible breakage. Aspects we investigate are:
- Diameter (the thinner the diameter has become, the more the cable is worn out)
- Wear both internal and external
- Zinc oxidation (indicated by a white residue on the cable)
- Corrosion
- Other destruction in and on the cable, such as welding drops or places where the cable has rubbed over a stationary disc
- Any fractures (type and number)
Types of fractures
Uit de vorm van de gebroken draden kun je goed afleiden wat de oorzaak was van de breuk. Een rechte breuk (a) is het teken van vermoeiing. Omdat er heel veel draden in een kabel zitten, mogen er volgens de ISO4309 meerdere van dit soort breuken in een kabel zitten. Wordt dat maximum aantal overschreden, dan
From the shape of the broken wires, you can easily deduce the cause of the break. A straight fracture (a) is a sign of fatigue. Because there are many wires in a cable, according to ISO4309, there may be several such breaks in a cable. If this maximum number is exceeded, the cable must be replaced.
Picture (b) is a sign of sudden force. This occurs when a load suddenly falls into the cable. For example, if the cable breaks on one side of a lift and the lift's weight falls into the other cable.
As in (c), a break is a sign of overload. This is when there has been too much load on the cable in a short time. You will need steel cables with a greater breaking force in the future. Or you can only use these cables for lighter loads. We also see this type of fracture in the tensile test in the lab.
We seldom actually see a fraction like (d). The fracture only looks like this when perfect material is overloaded.
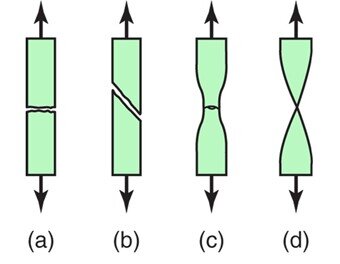
ISO4309
At the end of each laboratory test, we compare the results of the proven cables with the European standard EN-10218-1 and the international standard ISO 4309. The EN-10218-1 sets requirements for zinc weight, torsion and tensile strength. The ISO4309 sets requirements for how much the diameter has reduced, corrosion and wire breaks.
Each part is assigned a percentage. For example, if the cable diameter has decreased by more than 3.5% but less than 4.5%, then 20% rejection is attributed to it. At 100%, the cable is rejected. Even if the various components together achieve 100%.
Would you like to know more about our laboratory tests?
And whether this makes sense for your project? Please contact one of our branches.
Steel cable, make the right choice
Safe and efficient movement of loads, both vertically and horizontally. Get the maximum return from your installation with the certainty of business continuity. This requires the correct (application of) steel cable. You can read all about it in the Steel Cable File.